I would put a 1mH inductor in series with the input. That will give some separation, a reduction, of the energy the clamping device needs to handle. The value can be evaluated when running the board. This may not necessarily be the best approach, just one that I have used in the past.
I changed the schematic to what I would do. I would not try and clamp the power for the ignition coils. I would add a series inductor, then clamp the voltage for the regulator input as well as the driver chip.
Crude edit, but it is the best I can do.
A few years ago I designed the electronics for an electric motor driven sand and salt spreader. For sanding streets and parking lots in the winter. There was a conveyor motor and a spinner motor. The conveyor was a 3/4 hp motor. The rated running current was 55 amps at 12 volts. The electronics and firmware limited the starting current to about 120 Amps. The spinner motor was 1/3 hp. I the running current was about 30 Amps. The operator was able to set the speed of the spinner and conveyor with a Bluetooth app.
There was three mosfets for the spinner motor. Four (and another four for the reverse direction) on the conveyor. I used gate drivers like in the above design. I used 12 Ohm resistors in series with the gate of each mosfet.
The motors used created high power transients. I had three stages of filtering/clamping to deal with the transients. High power transorbs, resistor with series capacitor as a snubber circuit, and back emf diodes (big) across the motors. It was an interesting project.
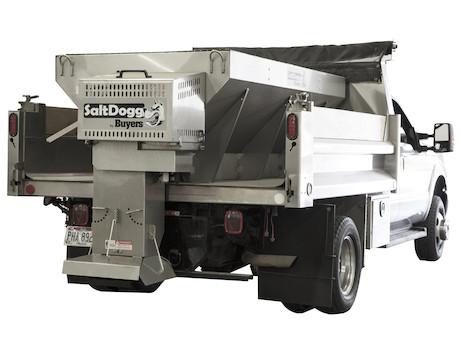